How to Ensure Sealing Performance of Medical Cold Forming Blister Foil

Aluminum blister foil packaging is currently the most widely used pharmaceutical packaging. How to improve sealing performance of medical aluminum foil? Learn more.
Aluminum blister foil packaging is currently the most widely used pharmaceutical packaging. Aluminum foil blister packaging not only has the advantages of good protection of medicines, fast production speed, low cost, small storage space, light weight, convenient transportation, good safety, etc., but also can provide patients with a dose of medicine packaging.
And there are text descriptions printed on the surface of the medical aluminum foil of the blister pack, which can effectively avoid the occurrence of wrong medicines for the drug dispensers in the process of distributing various tablets. To be sure, blister packaging will be the main way of packaging pharmaceutical tablets and capsules in the future. In pharmaceutical aluminum foil blister packaging, the heat sealing effect is very critical, which is related to the packaging quality of the entire pharmaceutical.
PTP blister packaging is to place the drug in the pit (called blister) and be sealed with a piece of aluminum foil that has been gravure printed and coated with a protective agent. Pharmaceutical blister packaging emerged from Europe as early as the 1930s. Due to the unique advantages of blister packaging, it has developed rapidly and extended to the outer packaging of injection boxes and medicines, health care products, and even food, cosmetics and other packaging fields. It has become the most important packaging form for future medicines and health care products.
The main materials of blister packaging are pharmaceutical blister aluminum foil, plastic hard sheet (polyvinyl chloride PVC) and adhesive. Aluminum foil is a sealing material sealed on a pharmaceutical polyvinyl chloride plastic hard sheet. Its surface can print text or patterns, and both sides have good printing adaptability. The aluminum foil is made of electrolytic aluminum with a purity of 99%, which is made by calendering and other treatment methods.
It is non-toxic and tasteless, has excellent electrical conductivity and shading properties, and has excellent properties such as extremely high moisture resistance, gas barrier and taste retention. In modern packaging, aluminum foil is used as a barrier material in almost all composite flexible packaging materials that require shading or high barrier properties. This is because aluminum foil has a highly dense metal structure, which can completely block any gas, water vapor and light, so it can protect the packaged objects most effectively.
The most widely used PTP plastic blister packaging is plastic hard sheet (referred to as PVC hard sheet). Since medicines are very sensitive to moisture and light transmission, plastic hard sheets are required to have good barrier properties against water vapor, light and odor. Although PVC has many advantages such as high quality and low price, it is not ideal in terms of moisture resistance, mildew resistance, water vapor resistance, and oxidation resistance.
In order to improve the defects of PVC, the production and application of PVC composite hard sheet has begun. This composite hard sheet is mainly composed of PVC hard sheet and another or several new polymer material films and sheets, through extrusion, compounding, coating, etc.
At present, the adhesives used in pharmaceutical blister packaging mainly include one-component adhesives and two-component adhesives. The adhesives used in the early days were single-component pressure-sensitive adhesives. The main components of pressure-sensitive adhesives were synthetic resin adhesives (including natural rubber, synthetic rubber, cellulose, and polyacrylates), adhesives (including rosin, Rosin esters, various petroleum resins, epoxy resins or phenolic resins, etc.), plasticizers (including chlorinated paraffins, phthalic acids), antioxidants, stabilizers, crosslinking agents, colorants and fillers, etc. With the improvement of hygienic requirements for pharmaceutical packaging materials, the amount of this one-component adhesive is gradually reduced.
At present, the single-component pressure-sensitive adhesive used in pharmaceutical packaging has been gradually replaced by two-component polyurethane adhesives. It is mainly composed of a main agent and a curing agent.
Cold forming blister foil is the carrier of the adhesive layer, and its quality has a great influence on the heat seal strength of the product. Especially the surface oil of the original aluminum foil can weaken the adhesion between the adhesive layer agent and the original aluminum foil.
If there is oil on the surface of the original aluminum foil and the surface tension is lower than 3.1×10-2μm, it will be difficult to achieve the ideal heat sealing strength, so the quality of the original aluminum foil must be strictly controlled.
Inquiry
Products Category
Latest Application
-
Why butter aluminum foil is neededButter aluminum foil blocks oxygen, moisture, and light, effectively preventing butter from oxidizing and spoiling, preserving nutrients, and significantly extending its shelf life. High-end products can see their sh application
-
Cables are usually composed of conductors, insulation layers, shielding layers, and sheaths. Aluminum foil for cable is generally located outside the insulation layer as part of the shielding layer. It fits tightly to the surface of the insulation la application
-
Aluminum Gold Foil Paper For Chocolate Wrapping
When is aluminum foil used for chocolate wrappingThe use of aluminium foil food for chocolate can be traced back to the early 20th century. In 1911, Swiss candy companies began to wrap chocolate with aluminum foil, gradually replacing the tin foil. T application
-
PVC Rigid Film and Aluminum Foil for Medicine Packaging
Haomei Aluminum provides different types of aluminum foil and plastic rigid films like PTP aluminum foil, cold forming foil, tropical foil, PVC rigid film, PE/PET film,etc. Best Price! Inquire now. application
-
Haomei Aluminum offers you different colors of air conditioner aluminum foil like hydrophilic aluminum foil, including1100/ 3003 /8006/8011 aluminum foil,etc. Learn more. application
Latest Blog
-
What Are Uses of Aluminum Foil Wrapping
Open your kitchen drawer, and that gleaming roll of aluminum foil always comes to the rescue in crucial moments—it's heat-resistant, locks in warmth, and seals out moisture. Many of our most common foods rely on it for intimate wrapping.BurgersWhether Blog
-
What Is Aluminum Foil Electrical Conductivity
In the industrial sector, the aluminum foil jumbo roll, thanks to its advantages such as lightweight, corrosion resistance, and easy processing, has become a fixture in the electronics, energy, and packaging industries. Electrical conductivity, as a Blog
-
What Is Specification of Aluminum Seal for Bottles
In the packaging industry, bottle sealing foil plays a crucial role, ensuring the quality of the product inside, extending its shelf life, and enhancing product safety.RequirementsGood barrier properties: This is a key characteristic of aluminum foil Blog
-
A Superstar in Packaging: Gold Wrap Aluminum Foil
On supermarket shelves, food packaging draped in gold always catches the eye instantly—the shimmering surface of chocolate boxes, the metallic sheen of tea cans, the luxurious texture of health product gift boxes—all owe their existence to the beauty of&n Blog
-
Aluminum Foil Winding in Transformer
Among the many components of a transformer, the winding is undoubtedly one of the key components, and its performance directly affects the overall performance of the transformer. Blog
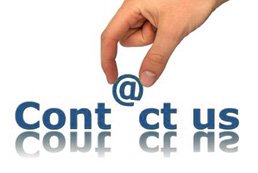
Haomei Aluminum CO., LTD.
Tel/Whatsapp: +86-15978414719
Email: sale@alumhm.com
Website: https://www.alumfoils.com
Xin'an Industrial Assemble Region,Luoyang,Henan Province,China
Office Add: 1103, No.14 Waihuan Road, CBD, Zhengzhou, China