Aluminum VS Copper Foil for Transformer Winding
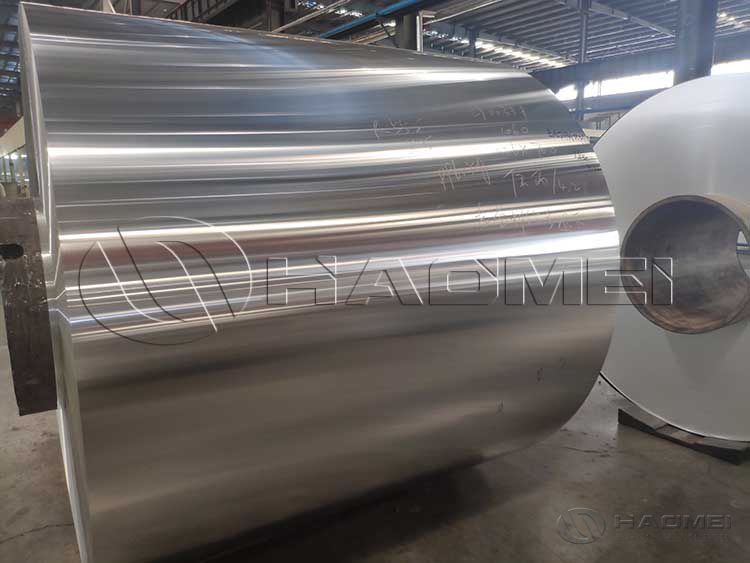
Aluminum foil and copper foil are two commonly used conductive materials for transformer winding, and they have their own characteristics. What are their differences? Learn more.
In the field of power transmission and conversion, transformers play a vital role. As the core component of transformers, the choice of materials for winding directly affects the performance, cost and service life of transformers.
At present, aluminum foil and copper foil are two commonly used conductive materials for transformer winding, and they have their own characteristics. In particular, the aluminum foil for transformer has gradually emerged in the market with their unique performance advantages.
1. Comparison of conductive properties
Copper foil is known for its excellent conductive properties. The conductivity of pure copper is as high as 58 MS/m (Mega Siemens per meter), which makes the resistance loss generated when the current is transmitted in the copper foil winding low, which can effectively improve the energy efficiency of the transformer.
In contrast, the conductivity of pure aluminum is about 35 MS/m, which is about 40% lower than copper. However, the aluminum foil used in transformer windings usually adopts special alloy formulas, such as 1 series pure aluminum (1060, 1070, etc.) and 3 series aluminum-manganese alloy (3003, 3105, etc.).
1 series pure aluminum like 1070 aluminum has high purity and good conductivity, while 3 series aluminum-manganese alloy significantly improves mechanical strength and corrosion resistance while maintaining certain conductive properties. Although its comprehensive conductive performance is still not as good as copper foil, it can also meet the conductive requirements of transformer windings through optimized design and appropriate increase in cross-sectional area.
2. Differences in mechanical properties
Copper foil has good flexibility and ductility. During the transformer winding process, it can easily adapt to complex shape and size requirements and is not prone to breakage or damage. Aluminum foil alloys also show their own advantages in mechanical properties, especially 3 series aluminum-manganese alloys.
Through alloying treatment, its tensile strength and hardness are significantly improved, and it can withstand certain mechanical stresses to ensure the structural stability of the winding during manufacturing and operation. However, the flexibility of aluminum foil is slightly inferior to that of copper foil, and when winding fine structure windings, the requirements for process and equipment are higher.
3. Cost and Economic Analysis
From a cost perspective, aluminum foil has a significant price advantage. The raw material price of aluminum is about one-third of that of copper, and the energy consumption of producing aluminum foil is relatively low, which makes it possible to significantly reduce production costs by using aluminum foil as a transformer winding material.
For large-scale power transformers, cost reduction means higher market competitiveness. Although the use of aluminum foil may require some adjustments in design, such as appropriately increasing the winding cross-sectional area to make up for the gap in conductivity, overall, aluminum foil alloys are an attractive choice in cost-sensitive application scenarios.
4. Comparison of corrosion resistance
In terms of corrosion resistance, aluminum foil alloy has a natural advantage. Aluminum will quickly form a dense aluminum oxide protective film in the air, which can effectively prevent further oxidation and corrosion, so that aluminum foil can still maintain good performance in harsh environments such as humidity, acid and alkali.
In contrast, although copper also has a certain corrosion resistance, it is prone to oxidation and sulfidation when exposed to a humid or sulfur-containing environment for a long time, resulting in the formation of corrosion products such as verdigris on the surface, affecting the conductivity and winding life. Therefore, in outdoor or highly corrosive environments, transformers with aluminum foil alloy windings have better durability.
5. Weight and heat dissipation performance
The density of aluminum is only one-third of that of copper. Using aluminum foil as a transformer winding material can significantly reduce the overall weight of the transformer, which is of great significance for some application scenarios that have strict requirements on weight, such as mobile substations and transformers for new energy vehicle charging piles.
In addition, the specific heat capacity of aluminum is higher than that of copper. Under the same heat generation conditions, the temperature rise of aluminum foil windings is relatively low, which helps to improve the heat dissipation performance of the transformer and extend the service life of the equipment.
Inquiry
Products Category
Latest Application
-
Why butter aluminum foil is neededButter aluminum foil blocks oxygen, moisture, and light, effectively preventing butter from oxidizing and spoiling, preserving nutrients, and significantly extending its shelf life. High-end products can see their sh application
-
Cables are usually composed of conductors, insulation layers, shielding layers, and sheaths. Aluminum foil for cable is generally located outside the insulation layer as part of the shielding layer. It fits tightly to the surface of the insulation la application
-
Aluminum Gold Foil Paper For Chocolate Wrapping
When is aluminum foil used for chocolate wrappingThe use of aluminium foil food for chocolate can be traced back to the early 20th century. In 1911, Swiss candy companies began to wrap chocolate with aluminum foil, gradually replacing the tin foil. T application
-
PVC Rigid Film and Aluminum Foil for Medicine Packaging
Haomei Aluminum provides different types of aluminum foil and plastic rigid films like PTP aluminum foil, cold forming foil, tropical foil, PVC rigid film, PE/PET film,etc. Best Price! Inquire now. application
-
Haomei Aluminum offers you different colors of air conditioner aluminum foil like hydrophilic aluminum foil, including1100/ 3003 /8006/8011 aluminum foil,etc. Learn more. application
Latest Blog
-
What Are Uses of Aluminum Foil Wrapping
Open your kitchen drawer, and that gleaming roll of aluminum foil always comes to the rescue in crucial moments—it's heat-resistant, locks in warmth, and seals out moisture. Many of our most common foods rely on it for intimate wrapping.BurgersWhether Blog
-
What Is Aluminum Foil Electrical Conductivity
In the industrial sector, the aluminum foil jumbo roll, thanks to its advantages such as lightweight, corrosion resistance, and easy processing, has become a fixture in the electronics, energy, and packaging industries. Electrical conductivity, as a Blog
-
What Is Specification of Aluminum Seal for Bottles
In the packaging industry, bottle sealing foil plays a crucial role, ensuring the quality of the product inside, extending its shelf life, and enhancing product safety.RequirementsGood barrier properties: This is a key characteristic of aluminum foil Blog
-
A Superstar in Packaging: Gold Wrap Aluminum Foil
On supermarket shelves, food packaging draped in gold always catches the eye instantly—the shimmering surface of chocolate boxes, the metallic sheen of tea cans, the luxurious texture of health product gift boxes—all owe their existence to the beauty of&n Blog
-
Aluminum Foil Winding in Transformer
Among the many components of a transformer, the winding is undoubtedly one of the key components, and its performance directly affects the overall performance of the transformer. Blog
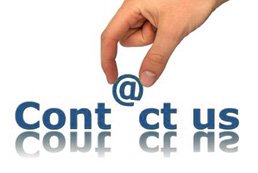
Haomei Aluminum CO., LTD.
Tel/Whatsapp: +86-15978414719
Email: sale@alumhm.com
Website: https://www.alumfoils.com
Xin'an Industrial Assemble Region,Luoyang,Henan Province,China
Office Add: 1103, No.14 Waihuan Road, CBD, Zhengzhou, China